Wear the rain
Generative modelling project mapping 3D generated geometry onto models of clothing. Predessor to later projects.
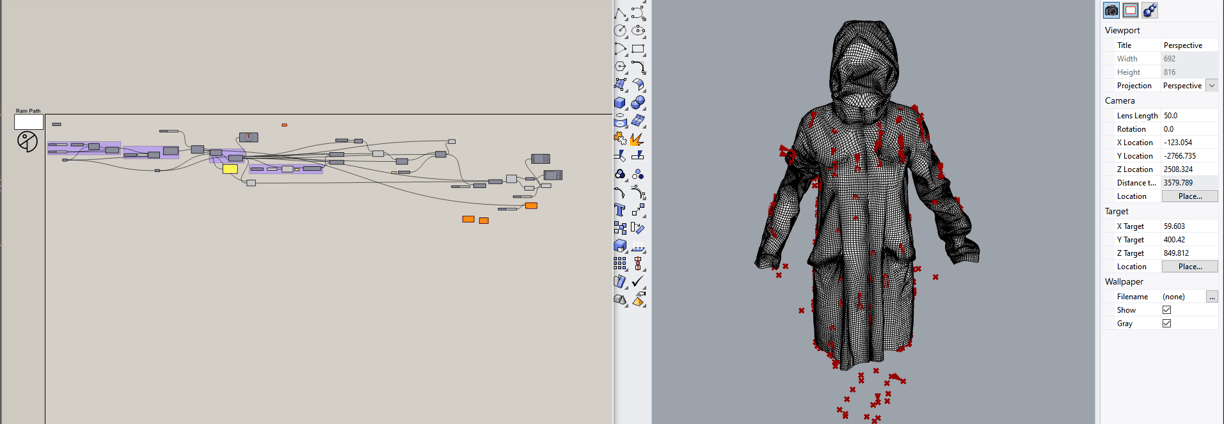
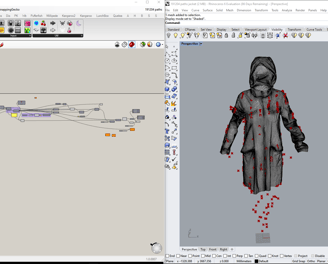
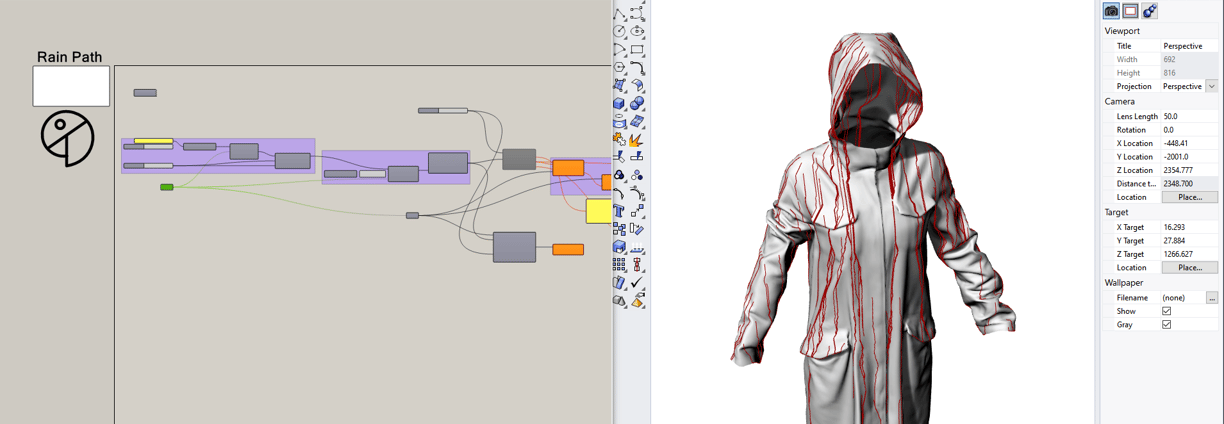
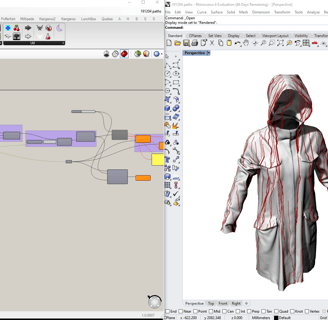
Using Grasshopper in tandem with CLO3D to create novel 3D fabrics
The development of 3D software aimed specifically at garment modelling has opened up new avenues of innovation in the creation of both conceptually interesting and technically advanced garments. Examples of this software include CLO3D, Optitex and Tuka3d.
These packages follow the same workflow as physical garment manufacturing, meaning that a 3D items is built up from a series of 2D pattern pieces. The integrity of each of these pieces is maintained even when 3D models are exported from the software. Taking advantage of this when using generative design software allows the creation of conceptually advanced products which are highly suited to manufacturing.
In traditional clothing manufacturing the feedback between the assembled product and the patterns is very limited, adjustments can be made and patterns re-cut but the final assembled product can have no effect on the graphic or texture of the pattern pieces. Using Grasshopper and CLO3D to create a feedback loop means that new garments can be more adventurous and technically capable.
The fabric components of the garment are modelled in CLO which uses physics modelling to simulate the material and draping of the item. This can then be imported as an OBJ into rhino, crucially it retains pattern piece integrity with each piece a separate mesh.
Complex modelling can then be carried out over the garment using generative or non-generative techniques. Being able to model directly onto the formed garment gives designers opportunity to create both extremely functional and powerful aesthetic structures. Furthermore, utilisation of generative techniques and further feedback loops at this stage present the opportunity to optimise geometry for specific goals in a way that was not previously possible for garments. Once this modelling is complete the new geometry is separated onto its relevant pattern piece. The grouped pattern pieces and geometries are then generatively flattened and recreated respectively, enabling the geometry to be printed directly onto the pre-cut pattern pieces which and then finally assembled into the realisation of the garment.
This technique offers many opportunities for both designers and manufacturers, from greater personalisation to functional optimisation. There is particular relevance when addressing sustainability concerns as fashion is increasingly linked to high Co2 emissions. The ability to feedback simulation results into pattern making data has the potential to unlock greater functionality from garments and reduce the need to replace them.
However, in order to be used widely barriers need to be overcome. The usability could be improved by cross platform compatibility and greater software robustness. However, the biggest barrier is manufacturing. 3D printing TPU directly onto PU fabrics has shown promising results in the creation of a true 3D fabric, which can offer the practicality and comfort of traditional fabrics and the geometrical freedom of solid structures. However, there are limitations on the types of garments which would use a PU fabric. Additionally, the size of the pattern piece is limited to the size of the bed on the printer which currently is not large enough for common garments.
Client: University project
Location: Bristol, UK
Date: 2018
Role: Designer & Project Manager